Exploring Cutting-Edge Foam Control Technologies for Lasting Practices
Exploring Cutting-Edge Foam Control Technologies for Lasting Practices
Blog Article
A Comprehensive Overview to Implementing Foam Control Solutions in Your Procedures
Reliable foam control is a vital element of operational effectiveness that typically goes neglected. Understanding the intricacies of foam generation can dramatically influence both efficiency and item high quality. By examining vital elements such as application compatibility and workers training, companies can maximize their foam monitoring initiatives.
Understanding Foam Challenges
Foam difficulties are a substantial problem across numerous markets, influencing operational effectiveness and item quality. The development of too much foam can impede procedures such as blending, transport, and storage, resulting in enhanced downtime and waste. In fields like food and beverage, drugs, and petrochemicals, foam can disrupt manufacturing lines, creating product incongruities and contamination dangers.
Moreover, foam can block tools functionality, leading to expensive repair work and maintenance. For example, in wastewater therapy, foam can interfere with clarifier operations, causing lower therapy effectiveness and regulatory conformity problems.
Recognizing the underlying reasons for foam generation is important for reliable management. Factors such as surfactants, temperature level variations, and frustration degrees can all add to foam manufacturing. Recognizing these components permits sectors to apply targeted techniques that minimize foam development while preserving product stability.
Kinds Of Foam Control Solutions

Mechanical remedies entail making use of gadgets such as foam skimmers or defoamers. These tools physically get rid of foam from the surface area of fluids, therefore preventing overflow and preserving optimum levels in tanks and activators. Chemical solutions, on the various other hand, include the application of defoaming representatives-- compounds that interrupt the foam structure, causing its collapse. These representatives can be silicone-based, natural, or aqueous, each offering distinctive benefits relying on the application setting.
Lastly, functional approaches concentrate on procedure adjustments. This may involve modifying tools specifications, such as temperature level and stress, or changing the circulation rates of fluids to reduce foam generation. Carrying out excellent housekeeping methods can also alleviate foam development by decreasing pollutants that contribute to foam security.
Picking the ideal foam control solution includes assessing the details demands of the operation, consisting of the kind of process, the qualities of the products involved, and safety factors to consider.
Selecting the Right Products
Selecting the appropriate foam control items needs a thorough understanding of the particular application and its unique difficulties. Factors such as the kind of foam, the environment in which it occurs, and the preferred result all play pivotal roles in product choice. Foam Control. In industries such as food processing, it is vital to select food-grade defoamers that abide with safety and security laws while properly taking care of foam.
In addition, think about the thickness of the fluid where the foam issue exists. Some items are created for low-viscosity applications, while others are tailored for thicker liquids. Compatibility with existing processes is one more crucial aspect; the picked foam control agents must integrate effortlessly without interfering with overall operations.
Another important aspect is the method of application. Some items might need dilution, while others can be used directly. Analyzing the simplicity of use and the needed dose can offer insights into the item's efficiency and cost-effectiveness.
Implementation Methods
Successful implementation strategies for foam control remedies call for an organized approach that straightens item option with operational demands. The primary step entails a detailed analysis of the procedures where foam takes place, identifying certain locations that require treatment. By involving cross-functional groups, consisting of visit our website engineering, high quality, and production guarantee, organizations can collect insights that notify the selection of one of the most efficient foam control items.
Following, it is critical to establish clear objectives for foam decrease, ensuring that these objectives are quantifiable and attainable. This may entail specifying acceptable foam degrees and the timelines for implementation. Educating employees on the homes and application approaches of selected foam control representatives is similarly important, as appropriate use is essential for optimal results.
Additionally, integrating foam control solutions right into existing process calls for careful preparation. Eventually, a well-structured technique will boost functional performance while efficiently handling foam-related challenges.
Monitoring and Examining Efficiency
Monitoring and assessing the performance of foam control options is necessary for ensuring that executed strategies produce the desired results. This process involves organized information collection and evaluation to assess the efficiency of foam control agents and methods. Trick performance indicators (KPIs) need to be established prior to execution, enabling a clear baseline against which to determine development.
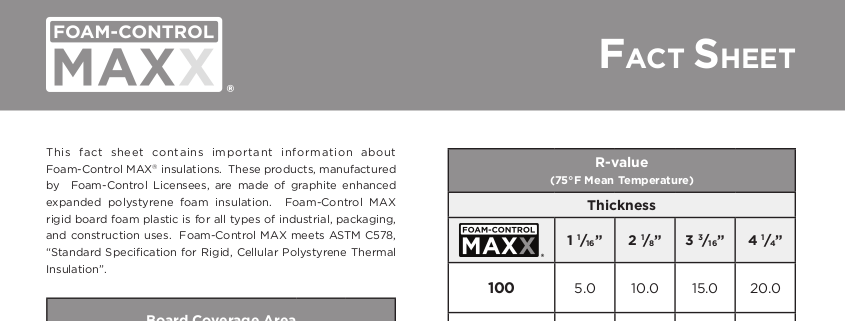
Reviewing performance likewise requires regular reviews of foam control treatments and representative efficacy. This can be achieved with sampling and testing, enabling operators to identify if existing remedies are satisfying functional demands. Additionally, it is vital to solicit responses from employee who communicate with these systems daily, as their insights can expose operational subtleties that quantitative data may neglect.
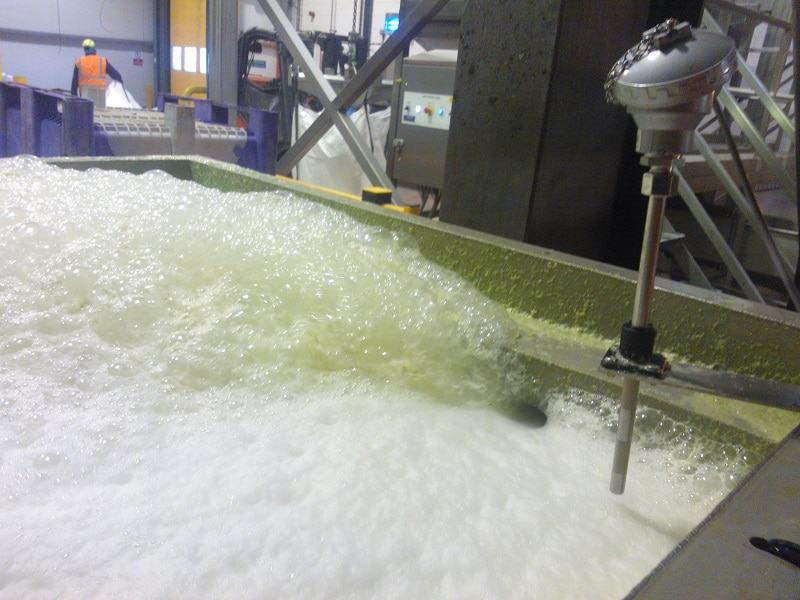
Inevitably, an organized tracking and analysis framework assists recognize required modifications, ensuring that foam control remedies continue to be reliable, cost-effective, and straightened with business goals.
Verdict
In conclusion, effective foam control remedies are vital for maximizing operational performance and preserving product high quality. A detailed understanding of foam obstacles, combined with the choice of proper items and implementation methods, assists in the effective management of foam generation.
Applying great housekeeping methods can also minimize foam development by lowering pollutants that add to foam security.
Selecting the right foam control items requires a thorough understanding of the particular application and its distinct challenges (Foam Control).Effective application techniques for foam control options need This Site an organized approach that aligns product option with functional needs.In conclusion, efficient foam control remedies are essential for maximizing operational effectiveness and keeping item top quality. An extensive understanding of foam obstacles, integrated with the choice of proper products and implementation approaches, facilitates the successful monitoring of foam generation
Report this page